Tunnel rudders were employed to overcome some of the
disadvantages of conventional rudders or directional propellers.
The semi-circular "shield" around the propeller's upper half ensures greater
protection and safety.
lt also enhances handling and thrust by channelling the jet in the direction required.
The two vertical rudder blades, which form the continuation of the shield, act as
"side walls".
They run below hull level thus ensuring, if needed, effective direction control by working
in turbulence-free waters. These side walls reach as far as the propeller diameter's outer
edge, so as to reduce the likelihood of damage when navigating in shallow waters.
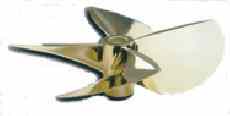  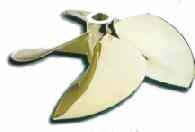
In addítion to the advantages of a conventional drive,
it provides increased surface propeller efficency without its penalizing limitations. Last
but not least, as the latest result of extensive investigatìon on wide speed range
planing hull drives, Sea Rider is currently employed both on pleasure and work vessels
(navy and passenger), thus becoming a landmark in the field of transmission.
The undewater exhaust system employed in the Sea Rider drive provides several
considerable advantages: reduction of noise and suppression of exhaust gases, which may
give serious problems in today's highiy powerful diesel engines. The ventilation of the
propeller's upper section provides smooth thrust progression when passing from underwater
to surface operating mode. |
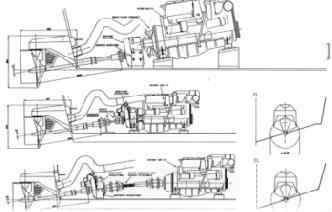 |
This gives the engine greater acceleration,
ensures good exhaust gas emptying (thanks to low pressure in front of the blades), reduces
the likelihood of exhaust pipe back pressure and does not require any silencer.
The "V" geometry of the Sea Rider body ensures that when the propeller's thrust
is reversed the resulting flow from the disk's upper half is channelled under the hull
without obstruction.
No efforts were spared in combining all of these features in order to produce a high
quality, cleanly stylish product.
Propeller: this type of propeller is a further advancement in the field of surface
propeller design. A consequence of the Sea Rider project, it has the ability to eliminate
one of the main drawbacks of this type of propeliers: difficult handling when going
astern.
Section: the back of the-blade features a concave surface towards the outer edge,
whose action delivers the necessary thrust when propeller rotation is reversed.
Efficiency: it was proved through numerous tests ín the Genoa University
cavitation tunnel. |